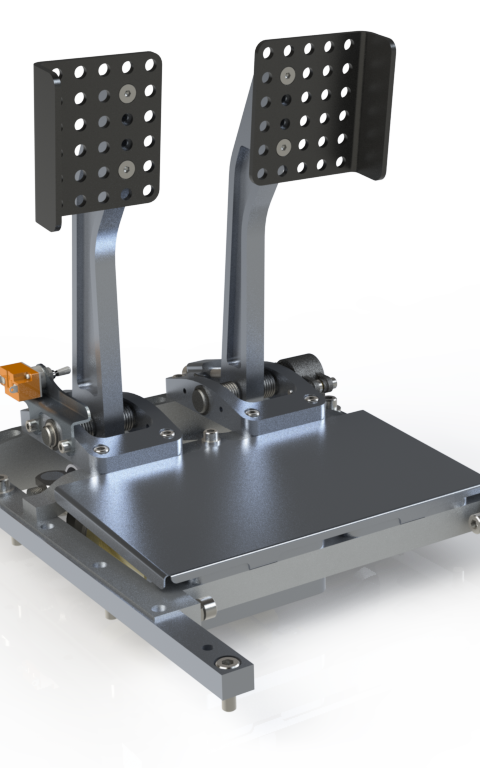
During my time as Lead Drivetrain Engineer at Leeds Gryphon Racing, I was tasked with coordinating the design and manufacture of lightweight parts and assemblies for both our ICE and electric cars. Here, it was crucial that all parts could be manufactured within time constraints and without exceeding a limited budget – an objective that I achieved by focusing on design for manufacture and assembly.
One of these assemblies was a modular pedalbox which was designed around the constraints of the breaking and throttle systems, considering both the competition rules and a 6-month deadline. The first step in this process was to evaluate the equipment, resources, and budget for the project to enable effective design for manufacture. Consequently, many of the parts utilised a waterjet cutting service for the primary manufacturing step, due to the relatively low cost, short lead time and convenience, followed by further manufacturing processes including folding and milling.
See below for some pictures of the designs and them implemented in the car at FS2022!
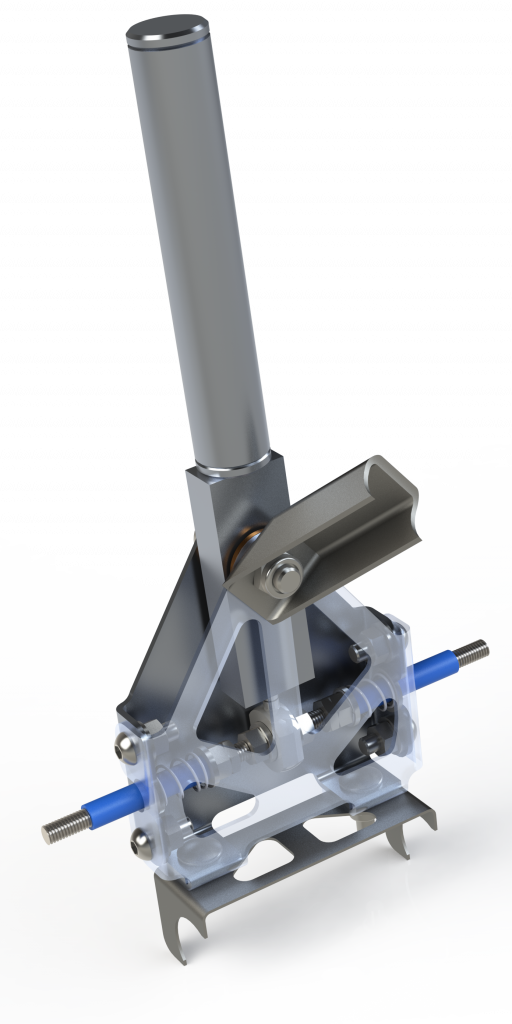